Защита от коррозии аппаратов переработки газа и нефтехимии.
Рисунок 1: Колонна С01 Астраханского ГПЗ ООО «Газпром Добыча Астрахань»
ООО «Газпром Добыча Астрахань», крупнейшее газоперерабатывающее предприятие ОАО «Газпром»,s добывает и перерабатывает природный газ. Доля сероводорода в добываемом газе составляет 26-28%. В процессе эксплуатации основного технологического оборудования, возникла проблема коррозионного и эрозионного износа и язвенной коррозии внутренней поверхности корпусов колонн абсорбера (Рис.1) очистки природного газа от сероводорода, с содержанием последнего до 28%. Глубина язв достигала 0,5-5мм, их диаметр — 4-32мм, а плотность 1-35 язв/дм². (Рис.2). Диаметр обечайки корпуса колонн («Крезо Луар») 4000мм, толщина стенки из стали А48FPSS – 105/72мм. Условия эксплуатации Рраб.=65/64,5 кгм/см², Траб.=92/49°С, среда: вода, сероводород, природный газ, амин.
Работы по восстановлению ранее производились методами наплавки с демонтажом колонны. При этом основные затраты ООО «Газпром Добыча Астрахань» несло из-за простоя производственной нитки на период демонтажа/монтажа и ремонтных работ. В ходе исследований были испробованы различные методы защиты поверхности, включая металлизацию, полимерные покрытия, экранирование, однако ни один из них не дал эффекта. Для выполнения работ по восстановлению внутренней поверхности колонны без ее демонтажа ООО «Газпром Добыча Астрахань» в 2001 г. обратилось к ООО «Технологические системы защитных покрытий». На основании проведённых исследований и испытаний было решено применить установку высокоскоростного газопламенного напыления Технологические системы защитных покрытий-HVOF для нанесения защитных покрытий нержавеющим сплавом на основе железа.
В рамках контракта ООО «Технологические системы защитных покрытий» с ООО «Газпром добыча Астрахань», совместно с ООО «Газпром ВНИИГАЗ» в 2003 г. была разработана технология и изготовлено уникальное роботизированное оборудование для нанесения защитного покрытия методом высокоскоростного газопламенного напыления внутренних поверхностей колонн без их демонтажа. В ходе работ было разработано и аттестовано покрытие колонн абсорберов.
Оборудование позволяет производить высокоскоростное газопламенное напыление путем использования энергии сверхзвуковой газовой струи, образующейся в результате сгорания газообразного пропана в воздухе. В процессе напыления частицы порошка нагреваются ниже температуры плавления, а скорость их достигает 800 – 900м/сек, при этом обеспечивается адгезия более 50 МПа, пористость менее 1%, а поверхность не нагревается более 150 °С.
Рисунок 2. Фрагменты поверхности абсорбера без покрытия
Рисунок 3: Нанесение металлических защитных покрытий внутри колонны С01 на Астраханском ГПЗ ООО «Газпром Добыча Астрахань»
Для повышения эффективности защитных свойств покрытия на него наносился полиуретан методом воздушного распыления на предварительно обработанную адгезивом поверхность.
В результате проведённых работ процесс коррозии остановлен. Данная технология включена как обязательная в регламент ежегодных планово-предупредительных ремонтов. Доказанный плановый интегральный экономический эффект от внедрения защитных покрытий колонн и емкостей за период с 2001 по 2007 год составил более пяти миллиардов рублей. Федеральная служба по экологическому, технологическому и атомному надзору одобрила проведение работ.
ООО «Газпром Добыча Астрахань» решило защищать оборудование методами напыления самостоятельно, для чего приобрело оборудование, лицензию на использование технологии, с помощью ООО «Технологические системы защитных покрытий» смонтировало и запустило участок напыления. ООО «Технологические системы защитных покрытий» продолжает выполнять сложные работы и разрабатывает новые технологии для ОАО «Газпром».
Все затраты на НИОКР, приобретение и запуск оборудования и технологий окупились менее чем за шесть месяцев за счет сокращения простоев, продления срока жизни и межремонтных периодов оборудования.
Защита от коррозии емкостей для производств с менее агрессивной средой производится путем напыления алюминия с последующим покрытием пропитывающим слоем, что позволяет с минимальными затратами эффективно и надолго защитить поверхность.
Рисунок 4: Нанесение металлических защитных покрытий на детали металлоконструкций методом электродуговой металлизации
Нанесение детонационных покрытий
Метод детонационного нанесения покрытий основан на высокоскоростном ударном взаимодействии нагретых до высоких температур частиц порошка напыленного материала с подложкой (рис. 5).
Рис. 5. Схема детонационной установки с внутренним смесеобразованием: 1 – клапан подачи ацетилена; 2 –клапан подачи азота; 3 – канал подачи порошка; 4 – свеча зажигания; 5 – ствол пушки; 6 – клапан подачи кислорода; 7 – мишень
Детонационная установка с внутренними смесеобразователями представляет собой водоохлаждаемый ствол длиной 1…1,8 м с внутренним диаметром от 10 до 40 мм. В ствол подается смесь кислорода и ацетилена вместе с порцией порошка. Взрываемая газовая смесь воспламеняется при помощи электрического импульса, и детонационная волна перемещается по стволу, ускоряя и нагревая порошок. Частицы порошка ускоряются до скорости 500…1000 м/с и ударяются в деталь, образуя пятно напыленного покрытия. Затем ствол очищается азотом, и процесс повторяется. Процесс напыления осуществляется циклически (4…10 циклов в секунду). Детонационные покрытия обеспечивают повышение эксплуатационных свойств и ресурса работы узлов, машин и механизмов, восстанавливают изношенные детали (до 1 мм на сторону).
Материалы покрытий:
- металлы и их оксиды, карбиды, бориды, нитриды;
- твердые сплавы;
- композитные порошки.
Комплекс детонационного напыления «ГРОМ-3М»
Комплекс «ГРОМ-3М» предназначен для восстановления дорогостоящих и дефицитных деталей машин, механизмов, работающих в условиях интенсивного износа (рис. 6).
Рис. 6. Комплекс детонационного напыления «Гром-3М»: 1 – стойка для установки пушки; 2 – напыляемая деталь (коленвал); 3 – трехствольная пушка с порошковым питателем
В состав оборудования входят:
- пушка детонационная;
- защитная звукоизолированная камера;
- манипулятор для перемещения деталей;
- стойка управления.
Комплекс «ГРОМ-3М» позволяет:
- восстанавливать изношенные поверхности коренных и шатунных шеек коленчатых валов двигателей внутреннего сгорания, а также любых тел вращения;
- наносить износостойкие покрытия с заданными свойствами;
- существенно повысить эксплуатационный ресурс восстановленных деталей;
- в 2…3 раза снизить затраты при ремонте оборудования за счет отказа от приобретения новых узлов и деталей машин и механизмов.
Технические характеристики
- Габаритные размеры напыляемых деталей:
- длина, мм 1700
- диаметр, мм 500
- Масса напыляемых деталей, кг не более 350
- Вертикальное перемещение пушки, мм 1900
- Скорость перемещения пушки, м/с 5…50
- Скорость вращения напыляемой детали, об./мин 1…75
- Скорострельность пушки, цикл/с 17
- Количество стволов, шт. 3
- Толщина наносимого слоя, мм 0,01…3
- Адгезия, кг/мм2 10…30
- Твердость наносимых слоев, ед. НRC до 65
- Рабочие газы:
«топливо» – пропан-бутан
«окислитель» – кислород
«продувка» – воздух
- Напряжение питания, В 3×380
- Потребляемая электрическая мощность, кВт не более 1
Просмотров:
1 423
Антикоррозионная защита выхлопных шахт ГПА.
Эффективно применение металлических покрытий при защите наружной и внутренней поверхностей металлических выхлопных труб шахт ГПА и дымовых газовых труб. Напыленный слой 200-250 мкм алюминия, покрытый сверху специальной пропиткой, при нагреве трубы до + 200°С диффундирует образует интерметаллидный алюмосилицированный слой, который не подвержен коррозии и сохраняет свои защитные свойства при температуре до + 700 °С.
В период с 2007 по 2009г. был проведен ряд опытно-промышленных испытаний покрытий в различных условиях, с целью применения для антикоррозионной защиты выхлопных шахт ГПА. Одним из первых, кто испытал в рабочих условиях газотермические покрытия, наносимые силами и по технологии ООО «Технологические системы защитных покрытий», стал ООО «Газпром Трансгаз Москва».
Рисунок 5: Выхлопная шахта ГПА
Рисунок 7: Выхлопная шахта ГПА, вид снаружи
Рисунок 6: Выхлопная шахта ГПА, вид снаружи
На фотографиях, представленных выше, отчетливо видны продукты коррозии, образовавшиеся в рабочих условиях выхлопных шахт компрессорных станций магистральных газопроводов ООО «Газпром Трансгаз Москва».
Рисунок 5: два образца-свидетеля с защитным покрытием после коррозионных испытаний, установлены внутри выхлопной шахты турбины № 22 ГТН-16М-1
На территории Давыдовской ГКС (г. Моршанск, Тамбовская обл.) были установлены четыре образца-свидетеля, установленных внутри двух выхлопных шахт турбин № 21 и № 22 ГТН-16М-1 (по два образца-свидетеля в каждую шахту) и пять образцов-свидетелей, установленных на наружных поверхностях двух выхлопных шахт турбин №21 и №. 22 ГТН-16М-1 и одной выхлопной шахты ГТК-25ИР ст. № 13
По окончанию в испытаний был произведен комиссионный разбор, в результате которого было установлено, что на нанесенном силами и по технологии ООО «Технологические системы защитных покрытий» покрытии на пластинах в условиях атмосферной и термохимической коррозии, т.е. в рабочих условиях выхлопных шахт компрессорных станций магистральных газопроводов ООО «Газпром Трансгаз Москва» следов коррозии не обнаружено, что подтверждает их пригодность для защиты выхлопных шахт и металлических дымовых труб от коррозии.
ОАО «Таганрогский завод «Красный котельщик» в ноябре 2007 г. провел испытания термостойкости покрытия. Испытание подтвердило стойкость покрытия к кратковременному нагреву до температур, приближающихся к температуры плавления алюминия без его разрушения и отслоения. ООО «Газпром трансгаз Москва» на территории Давыдковской ГКС, Моршанского УМГ с ноября 2007 г. по июль 2008 г. (всего 8,5 месяцев) провело испытания образцов с покрытиями внутри и снаружи выхлопных шахт турбин. Признаков коррозии не обнаружено. Испытания показали пригодность покрытия для защиты выхлопных шахт от коррозии.
Общие сведения о методе газопламенного напыления
В основе метода лежит использование тепловой и кинетической энергии для повышения реставрационных, функциональных или декоративных характеристик изделия. Присадочный материал для выполнения работ выпускают в следующих формах:
- проволока;
- прутки;
- порошок.
Для каждого вида существует своя сфера применения. Например, для реставрации деталей машин и механизмов специалисты рекомендуют использовать порошки. В отличие от проволоки они позволяют менять состав покрытия, что способствует повышению качества напыляемого слоя.
Процедура обработки изделия состоит из следующих этапов:
- Порошок подают в зону термической обработки. Он может поступать по каналам питателя или подаваться с внешней стороны горелки.
- Под действием высокой температуры присадочный материал оплавляется, приобретая пластичные свойства.
- Газ выполняет функции переноса состава на обрабатываемую поверхность. Летящие частицы перемещаются с большой скоростью – она может достигать 160 м/с.
- Распыленный материал формирует защитный слой при взаимодействии с поверхностью.
Проволока или прутки подаются в зону термической обработки с помощью роликового механизма. Средняя величина сечения присадочного материала составляет 3 мм. При обработке больших площадей для повышения производительности допустимо использовать проволоку диаметром до 7 мм.
Как было указано выше, температурная обработка осуществляется за счет тепловой энергии, которая образуется при сгорании горючего газа в кислородной среде. Наилучших результатов можно добиться при использовании ацетилена. Его температура горения варьируется в пределах 3100–3200 ºC. Для сравнения приведем аналогичные характеристики доступных заменителей:
Вид горючего газа | Теплота сгорания, кДж/м³ | Температура пламени в кислородной среде, ºC | Расход кислорода, м³/ч |
Ацетилен | 52800 | 3100-3200 | 2,5 |
Водород | 10060 | 2100–2500 | 0,5 |
Метан | 33520 | 2000–2700 | 2,03 |
Пропан | 87150 | 2400–2700 | 5,15 |
Бутан | 116480 | 2400–2700 | 6,8 |
Тип пламени определяется в зависимости от состава смеси:
- окислительное;
- нормальное;
- восстановительное.
Во втором случае соотношение газов паритетное. Окислительное пламя характеризуется избытком кислорода, а восстановительное – горючего вещества.
Метод газопламенного напыления обладает массой преимуществ:
- Благодаря малому тепловому воздействию на обрабатываемую заготовку существует возможность нанесения покрытия практически на любой материал: стекло, пластик, фарфор и даже дерево или бумагу. Другие методы модификации поверхности предназначены преимущественно для изделий из металла.
- В процессе обработки заготовка не подвергается тепловой деформации и не меняет своих параметров.
- С помощью установок для газопламенного напыления можно обрабатывать заготовку различными составами. Это позволяет придавать поверхности различные свойства без замены оборудования.
- Неограниченный размер обрабатываемой площади. Другие способы металлизации ограничены различными факторами: для цементации – размером печи, для электролитического осаждения – габаритами емкости с раствором.
- Низкая себестоимость обработки. Лучше всего эффект проявляется при газопламенном напылении больших площадей.
- Большая толщина покрытия позволяет использовать метод для реставрации различных деталей. Припуск под обработку не превышает 0,7 мм.
- Простота рабочего оборудования и его мобильность дает возможность применения газопламенного напыления в труднодоступных местах. Технологическая операция также не отличается особой сложностью.
- Благодаря широкому выбору присадочных материалов можно получить изделие с заданными свойствами, не прибегая к прочим методам модификации поверхности.
Естественно, имеются и недостатки:
- Газопламенное напыление малоэффективно при обработке мелких деталей. Это связано с высоким коэффициентом расхода присадочного материала.
- Тяжелые условия производства. Для предварительной подготовки изделия выполняют пескоструйную обработку, что приводит к повышенному уровню запыленности рабочего участка.
- В процессе напыления мелкие частицы состава остаются в воздухе. По этой причине к производственным помещениям предъявляют повышенные требования по системе вентиляции.
Электродуговая металлизация (ЭДМ)
Принципиальная схема электродуговой металлизации показана на рисунке 1.11. Через два канала в горелке непрерывно подают две проволоки (диаметром 1,5-3,2 мм), между концами которых возбуждается дуга, за счет тепла которой и происходит расплавление проволоки.
Расплавленный металл подхватывается струёй сжатого воздуха, истекающего из центрального сопла электрометаллизатора, распыляется и в виде жидких капель переносится на поверхность напыляемой детали.
Схема электродуговой металлизации
Рисунок 1.11 – Схема дугового напыления:
1 – сопло; 2 – место ввода напыляемого материала (проволоки);
3 – место подачи сжатого воздуха
Производительность процесса электродуговой металлизации (ЭДМ) чрезвычайно высока, например, можно напылять стальное покрытие с производительностью до 36 кг/ч, цинковое покрытие – до 1,2 кг/мин. При использовании в качестве электродов проволок из двух различных металлов можно получить покрытие из их сплава.
Такого рода сплавы называют псевдосплавами. Эксплуатационные расходы при электрометаллизации небольшие. Процесс дугового напыления хорошо поддаётся автоматизации.
Краткие характеристики покрытия:
- Пористость покрытия, 5-20 %;
- Прочность сцепления покрытия с основой (адгезия), 3,0–5,0 кг/ мм² ;
- Толщина напыленного слоя, 0,5 –15 мм.
Где используют плазменную металлизацию
Поскольку напыляемым материалом может служить практически любой сплав или металл, ионно-плазменное напыление широко используют в различных отраслях промышленности, а также для проведения ремонтно-восстановительных работ. Любой металл в виде порошков подается в плазменные установки, где под воздействием высокотемпературной плазмы расплавляется и проникает в обрабатываемую металлическую поверхность в виде тонкого слоя напыления. Сферы применения диффузной металлизации:
- детали для авиационной, космической и ракетной промышленности;
- машиностроительное оборудование и энергетическая отрасль;
- металлургическая и химическая отрасль промышленности;
- нефтедобывающая, нефтеперерабатывающая и угольная отрасль;
- транспортная сфера и производство приборов;
- ремонт и реставрация машин, оборудования, изношенных деталей.
Когда струя плазмы и порошков проходит по электродуге и осаживается на обрабатываемой поверхности, образованный слой приобретает важные качественные и эксплуатационные характеристики:
- жаростойкость;
- жаропрочность;
- коррозийную устойчивость;
- электроизоляцию;
- теплоизоляцию;
- эрозийную прочность;
- кавитационную защиту;
- магнитные характеристики;
- полупроводниковые свойства.
Газопламенное напыление: принцип действия и область применения
Суть газопламенного напыления заключается в формировании из исходного материала частиц раскаленного металла и переноса их на требуемую поверхность при помощи сжатого воздуха. Остывая, частицы формируют слой на выбранной поверхности.
В газопламенном напылении используется несколько видов сплавов напыляемого материала, каждый из которых позволяет достичь требуемых параметров созданного покрытия, таких как износостойкость и устойчивость к коррозии. В данной технологии активно используются: никелевые, цинковые, медные, железные, алюминиевые и другие сплавы, обладающие необходимыми свойствами. Исходный материал также отличается еще и по форме, в которой он подается. Стоить отметить, что температура плавления выбранного материала ниже, чем температура используемого пламени. Данное свойство гарантирует однородность наносимого слоя.
Технология газопламенного напыления
Технология проволочного газопламенного напыления, которую наиболее широко используют в промышленности, должна отвечать следующим требованиям.
Сжатый воздух, используемый для распыления расплавленной проволоки, должен быть сухим и не содержать масла. Давление сжатого воздуха должно быть не менее 0,4 МПа (4 физических атмосферы).
Перед напылением необходимо тщательно осмотреть поверхность. Если в результате осмотра установлено, что на ней имеются следы влаги, окисная пленка, окалина и другие загрязнения, необходима вторичная обдувка абразивными материалами. Первый слой покрытия напыляют в течение 4 часов после обдувки. Окончательное напыление покрытия до требуемой толщины должно быть проведено не более чем через 8 часов после предварительной обработки.
Зажигать горелку и выводить ее на рабочий режим необходимо вдали от напыляемой поверхности. Расстояние от горелки до поверхности детали обычно составляет 75…250 мм. Выбор величины этого расстояния зависит от напыляемого материала и диаметра проволоки, а также от свойств напыляемого покрытия. При очень малом расстоянии может возникнуть опасность коробления основы под действием термических напряжений. Когда же расстояние слишком большое, температура летящих частиц снижается, что приводит к образованию рыхлого покрытия и уменьшению прочности сцепления с основой, что может вызвать отделение покрытия от основы.
При порошковом напылении керамики расстояние от среза сопла горелки до основы составляет 150…200 мм, а в случае напыления пруткового материала это расстояние около 75 мм.
Наибольшая деформация напыляемых частиц при соударении с поверхностью основы происходит, если горелка установлена относительно нее под углом 90°. Когда невозможно обеспечить этот угол, покрытие получается с несколько худшими характеристиками. Допустимый угол наклона горелки, при котором можно наносить покрытие, составляет не менее 45°.
При напылении режим работы горелки, скорость перемещения и расстояние напыления должны поддерживаться постоянными. Обычно скорость перемещения горелки или основы при напылении на плоские поверхности составляет от 10 до 25 м/мин, а шаг перемещения горелки – 6…12 мм.
В случае перегрева поверхности основы при напылении происходит снижение прочности сцепления покрытия. Как правило, температура поверхности напыляемой детали не должна превышать 260 °С. Для контроля температуры основы можно воспользоваться, например, термопарами, термокарандашами или термокрасками, которые наносят на деталь в непосредственной близости от места напыления. Для предотвращения перегрева при напылении обрабатываемую основу можно охлаждать воздухом.
При температуре напыляемой поверхности, близкой к 0 °С и ниже, проводить напыление не рекомендуется, так как покрытие может отслоиться. Для того чтобы покрытие не растрескалось, необходимо предварительно нагреть основу до температуры 100…120 °С. От способа предварительной обработки основы в значительной степени зависит толщина наносимого покрытия. Нарезка резьбы на напыляемой поверхности позволяет наносить более толстые покрытия по сравнению с подготовкой поверхности обдувкой абразивными материалами.
При механическом перемещении напыляемого изделия или горелки процесс напыления принимает более устойчивый характер и покрытие можно получить более однородным. Для напыления на валы часто используют токарные станки. Обычно в этих случаях горелку устанавливают на суппорте. После напыления на этом же станке, не вынимая детали, можно произвести ее обточку или шлифование. При напылении покрытий на большие партии изделий процесс напыления желательно автоматизировать.
Покрытие, полученное после напыления, по своей структуре является в значительной степени пористым. Пористость его можно в некоторых случаях эффективно использовать. Заполнять поры можно путем нанесения на покрытие слоя краски, пропиткой покрытия специальными составами или проплавлением его, если оно получено из самофлюсующихся сплавов. Для улучшения механических свойств и термостойкости покрытия его можно подвергнуть также термической обработке. Однако наиболее широкое применение находят плотные покрытия.
Дополнительная комплектация
- горелки для внутреннего напыления (600, 1000 и 1500 мм) (рис. 11).
- соединительные газовые рукава для горелки внутреннего напыления.
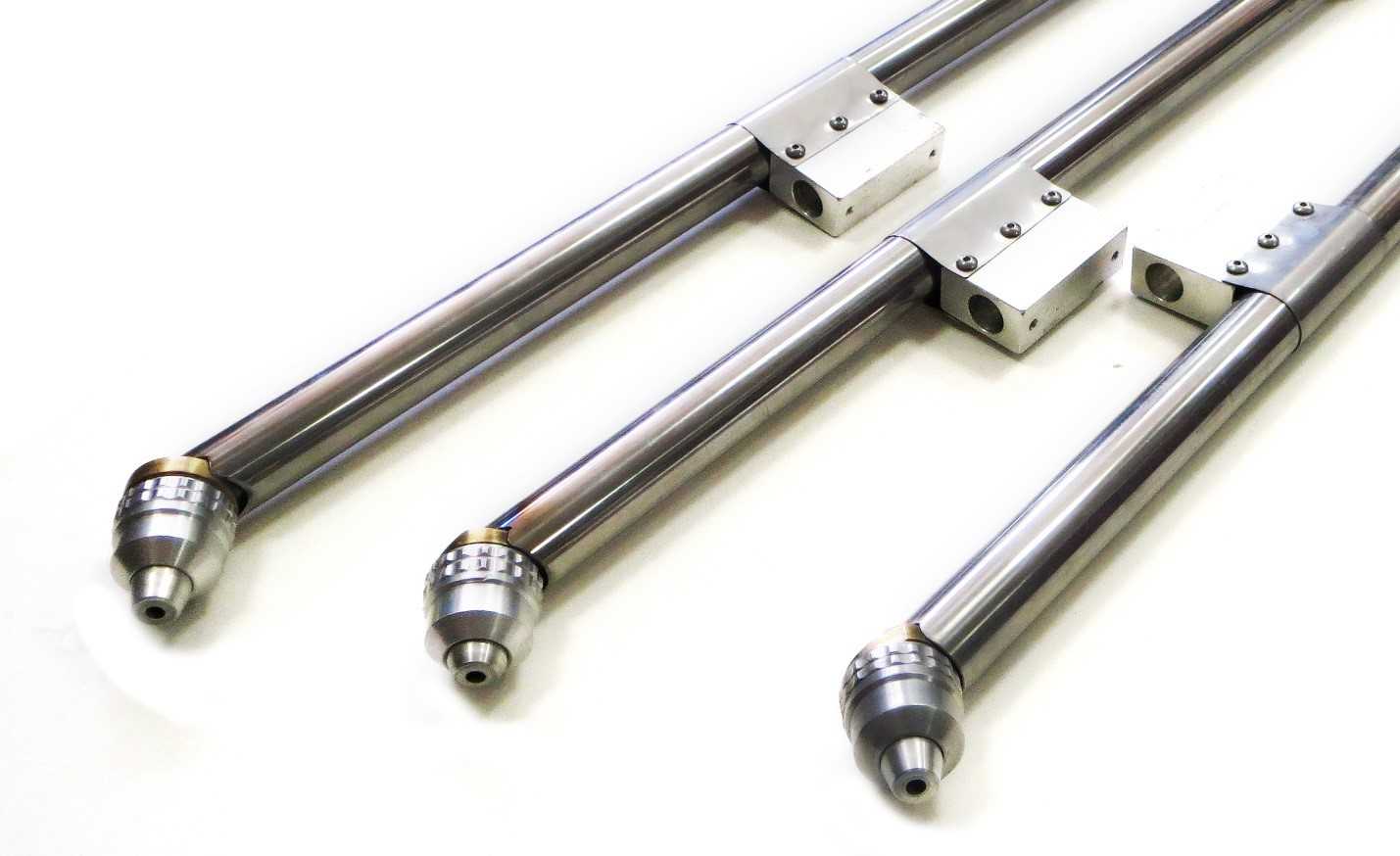
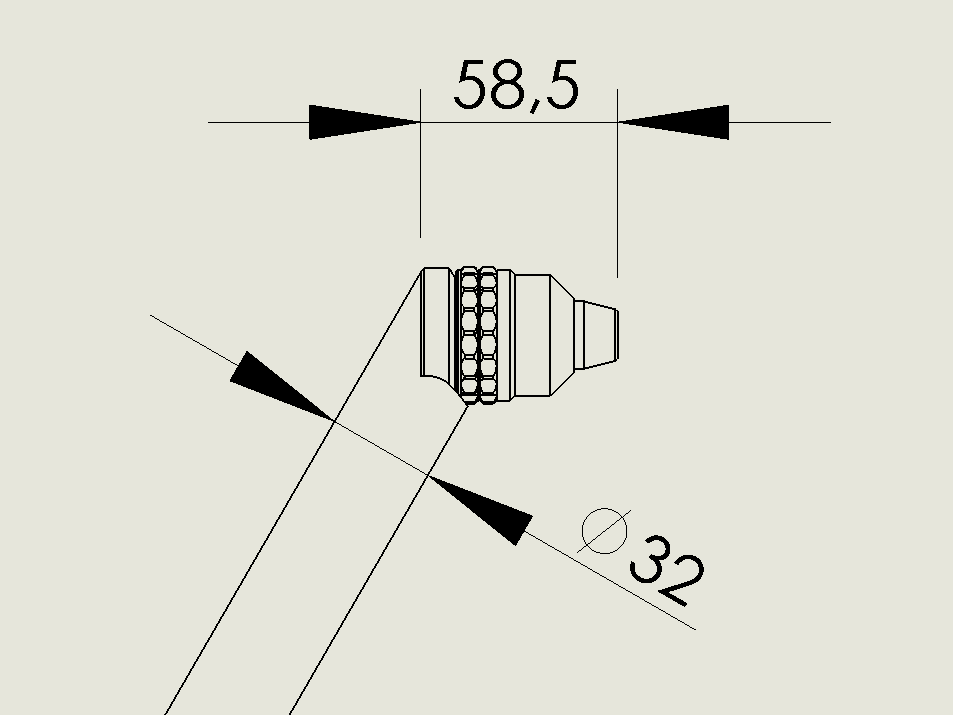
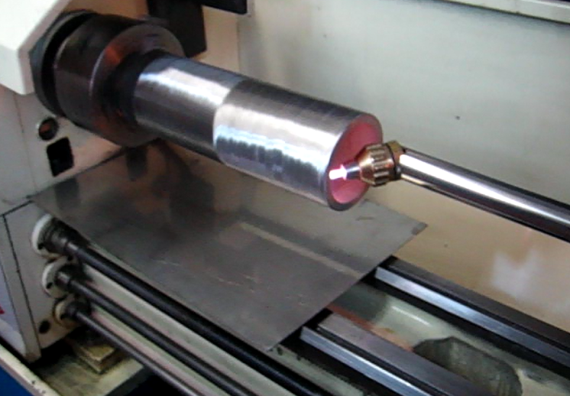
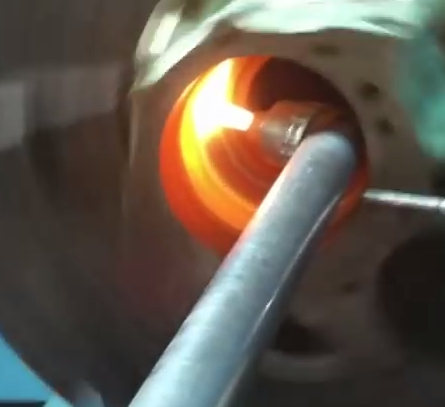
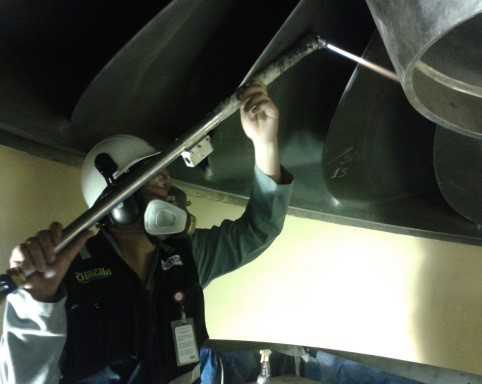
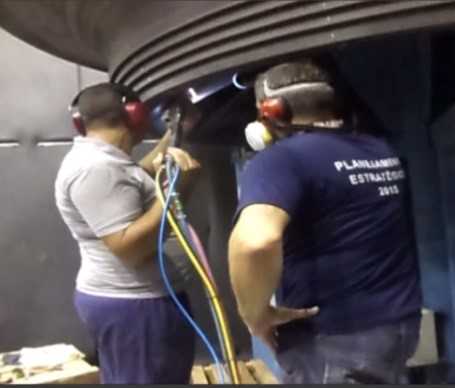
Установка HVOF-TERMIKA-3 отличается от аналогов удобством, простотой обслуживания, компактностью и надежностью и обеспечивают напыление тех же покрытий, что и системы, которые стоят в десятки раз дороже. Установка может использоваться как на крупных, так и небольших предприятиях, связанных с упрочнением или восстановлением деталей.
«Плазмацентр» предлагает
- услуги по восстановлению деталей, нанесению покрытий, напылению в вакууме, микроплазменному напылению, электроискровому легированию, плазменной обработке, аттестации покрытий, напылению нитрида титана, ремонту валов, покрытию от коррозии, нанесению защитного покрытия, упрочнению деталей;
- поставка оборудования для процессов финишного плазменного упрочнения, сварки, пайки, наплавки, напыления (например, газотермического, газопламенного, микроплазменного, высокоскоростного и детонационного напыления), электроискрового легирования, приборов контроля, порошковых дозаторов, плазмотронов и другого оборудования;
- поставка расходных материалов, таких как сварочная проволока, электроды, прутки для сварки, порошки для напыления, порошки для наплавки, порошки для аддитивных технологий, проволока для наплавки и другие материалы для процессов сварки, наплавки, напыления, аддитивных технологий и упрочнения;
- проведение НИОКР в области инженерии поверхности, трибологии покрытий, плазменных методов обработки, выбора оптимальных покрытий и методов их нанесения;
- обучение, консалтинг в области наплавки, напыления, упрочнения, модификации, закалки.
Свяжитесь с нами по телефонам: +7 (812) 679-46-74, +7 (921) 973-46-74, или напишите нам на почту: office@plasmacentre.ru
Наши менеджеры подробно расскажут об имеющихся у нас технологиях нанесения покрытий, упрочнения, восстановления, придания свойств поверхности, а также о стоимости услуг компании.
Преимущества
- высокая универсальность процессов, позволяющая наносить покрытия широкого функционального назначения, а также восстанавливать размеры изношенных деталей;
- малое термическое воздействие на напыляемую основу (интегральная температура нагрева деталей при напылении не превышает 150°С), что позволяет исключить нежелательные структурные превращения в ней и избежать деформаций;
- нанесение покрытий на детали, изготавливаемые практически из любого материала;
- отсутствие ограничений по размерам напыляемых изделий;
- нанесение покрытий на локальные поверхности;
- нанесение многослойных покрытий разнородными материалами;
- высокая технологичность процесса, в связи с гибкостью регулирования параметров режима;
- получение регламентируемой однородной пористости покрытия для использования в условиях работы со смазкой поверхностей скольжения;
- положительное влияние на усталостную прочность основы, за счет получения при напылении слоистой структуры покрытия;
- нанесение равномерного покрытия с минимальными припусками для последующей механической обработки;
- эксплуатация, в отдельных случаях, напыленных деталей без последующей механической обработки;
- использование напыления для формообразования деталей или аддитивных процессов (напыление производят на поверхность формы-оправки, которую после окончания процесса удаляют, и остается оболочка из напыленного материала);
- высокая производительность и автоматизация процесса.
Преимущества газопламенного напыления
- Сверхзвуковое (высокоскоростное) газопламенное напыление металла можно проводить на деталях различной конфигурации поверхности и степени сложности.
- В качестве напыляемого материала можно использовать металлы и полимеры с низкой пластичностью.
- Простота в восстановлении нанесенного покрытия.
- Отсутствие деформации поверхности при напылении.
Также очень широко сейчас применяется технология высокоскоростного (сверхзвукового) газопламенного напыления (HVOF). В данном способе при нанесении порошкового материала используются сверхзвуковые скорости. Изменение скоростного режима привело к тому, что данный способ нецелесообразно применять вручную, так как отдачу невозможно контролировать на таких скоростях. Поэтому для нанесения напыления требуются автоматизированные установки, которые способны нанести однородный слой нужной толщины и при этом выдержать отдачу. Увеличение скорости также повлияло на напыляемый материал. В данной технологии активно используют сплавы железа и никеля, а также карбиды.
Данные методы газопламенного напыления широко используются при восстановлении геометрической формы элементов различного оборудования, валов двигателей, нестандартных деталей и др. Также в спектр применения входит нанесение износоустойчивых и антикоррозийных покрытий, увеличивающих срок службы различных материалов.
Технология напыления
Важным вопросом технологии напыления является скорость подачи напыляемого материала. При недостаточной скорости образуются слишком мелкие расплавленные частицы цинка, которые быстро охлаждаются во время полета к покрываемой детали, что приводит к снижению прочности сцепления покрытия и коэффициента полезного использования напыляемого материала. К таким же результатам приводит и слишком большое (свыше 200 мм) расстояние от напыляемого изделия до горелки — покрытие получается рыхлым и непрочным.
При превышении скорости подачи увеличивается зона расплавления проволоки, размер частиц и степень их окисления, что снижает защитные свойства покрытия. Для улучшения сцепления цинкового покрытия наиболее эффективным методом является подогрев детали (оптимально до 150-170°С).
На качество металлизационного цинкового покрытия оказывает влияние состав газа в пламени горелки. При избытке кислорода происходит повышенное окисление расплавленных частиц цинка, а покрытие приобретает повышенную твердость и хрупкость. При избытке горючего газа в пламени образуются более пористые покрытия.
При таком цинковании стальных изделий для уменьшения пористости покрытия обычно наносят несколько слоев цинка (по 30-50 мкм в каждом слое).
Вместо газовой горелки можно применять распыление и расплавление цинка за счет электрической дуги.
Цинковые покрытия, нанесенные таким способом, являются очень пористыми, поэтому под слоем цинка протекают процессы окисления металла-основы. Характер покрытия хорошо виден на рис.2.6. Эти процессы идут очень медленно (как-никак, катодная защита), но образуются продукты коррозии железа коричневого цвета, и изделия приобретают очень неряшливый вид.
Для уменьшения пористости покрытия разработаны и все более широко применяются методы обработки поверхности путем разгона порошков струей сжатого воздуха через сопла Лаваля до сверхзвуковых скоростей. Частица, разогнанная до сверхзвуковой скорости, при ударе о поверхность мгновенно останавливается, ее кинетическая энергия превращается в тепловую, она расплавляется и прилипает к поверхности. В этом случае пористость покрытия и степень окисления порошка уменьшается в несколько раз.
Рис. 2.6. Увеличенная фотография среза цинкового покрытия, полученного методом газопламенного напыления.
Недостатком метода порошкового напыления, кроме высокой пористости покрытия, является невозможность получения качественного (одинакового по толщине) покрытия на большинстве деталей. Узкие щели, тупиковые полости, наконец, внутренняя поверхность — все это участки, которые невозможно покрыть качественно. Разработаны и существуют специальные установки для напыления внутренней поверхности однотипных предметов (например, буровых труб), но все это не решает проблемы.
Возможно Вас так же заинтересуют следующие статьи:
- Рекомендации проектировщику при использовании горячего цинкования
- Доработка оцинкованных изделий согласно ГОСТ 9.307-89
- Экология гальванического производства
- Требования к металлу в процессе цинкования металлоконструкций
- Модифицированные гальванические покрытия